ASME PCC-1:2000 pdf free download CUIDELINES FOR PRESSURE BOUNDARY BOLTED FLANGE JOINT ASSEMBLY
5 ALIGNMENT OF MATING sURFACES
Ensure flanges are aligned both axially and rota-tionally to the design plane within engineering designparameters without use of excessive force. Reportany questionable misalignment.
Appendix E provides a recommendation for align-ment tolerances.
6 INSTALLATION OF GASKET
Place a new gasket in position after determiningthe absence of unacceptable imperfections ordamage.
(a) Verify that the gasket complies with the dimen-sional (oD.ID, thickness) and material specifica-tions.
(b)Position the gasket to be concentric with theflange ID,taking suitable measures to ensure thatit is adequatelysupported during the positioningprocess. No portion of the gasket should projectinto the flow path.
(c) Ensure that the gasket will remain in placeduring the joint assembly process; a very light dustingof spray adhesive on the gasket (not the flange) maybe used. Particular care should be taken to avoidadhesive chemistry that is incompatible with theprocess fluid or could result in ‘stress corrosioncracking or pitting of the flange surfaces. Do notuse tape strips radially across the gasket to hold itin position. Do not use grease.
7LUBRICATION OF “wORKING” SURFACES
With one exception,liberally coat all internal andexternal thread surfaces and nut/washer faces withappropriate lubricant; the exception is: lubricant isnot to be applied to these “working”~ surfaces forthe initial tightening of new, coated bolts/nuts [seeNote (3) of Table iM/Table 1]. The torque valuesfor new, coated bolts/nuts shown in Table 1M/Table1 do not consider lubrication other than that providedby the bolt/nut coating [see Note (2y of Table 1M/Table 1]. Do not apply lubricant to the gasket orgasket-contact surfaces.
(a)Ensure that the lubricant is chemically compat-ible with the bolt/nut/washer materials and the pro-cess fluid. Particular care should be taken to avoidlubricant chemistry that could result in stress corro-sion cracking.
(b)Ensure that the lubricant is suitable for theexpected service temperature(s).
(c) While it is recognized that the inherent lubric-ity of new coated bolts results in less torque beingrequired during the first tightening application toachieve a given level of tension in the bolt (seeTable 1M/Table 1), the major long-term value ofcoated bolts is to promote ease of joint disassembly[see paras.8.2.1 and 15,and Note (3) of Table1M/Table 1].
8INSTALLATION OF BOLTs
lnstall bolts and nuts hand-tight,then“snug up”to 15 N-m (10 ft-lb) to 30 Nm (20 ft-lb), but notto exceed 20% of the Target Torque (see para. 12).lf nuts will not hand tighten,check for cause andmake necessary corrections.
8.1 Bolt/Nut Specifications
Verify compliance with bolt and nut specifications[materials,diameter,length of bolts,thread pitch,and nut thickness equal to the nominal bolt diameter(heavy hex series nuts)].
8.2 Bolt Lengths
Check bolts for adequate length. Section vl,Division 1 of the ASME Boiler and Pressure VesselCode (1998 Edition,1999 Addenda) requires thatnuts engage the threads for the full depth of thenut (see para. UG-13). The ASME B31.3,ProcessPiping Code (1 999 Edition),has a similar provisionbut considers the nut to be acceptably ehgaged ifthe lack of complete engagement is not more thanone thread (see para. 335.2.3). See para. 10.1(c) ofthis document if use of hydraulic bolt tensioners isplanned.
8.2.1 Corrosion of excess threads can hinder jointdisassembly.A practice that facilitates joint disassem-bly (see para. i5) is to fully engage the nut on oneend (no bolt projection beyond the nut) so that allexcess threads are located on the opposite end; theexcess threads should not project more than 13 mm( ‘/2in.) beyond the nut, unless required for the useof hydraulic bolt tensioners [see para. 10.1(c)].
9 NUMBERING OF BOLTS
Number each bolt location 1 through N in aclockwise sequence (where N is the total numberof bolts for the flange).An alternative bolt numberingmethod is described in Appendix F.
ASME PCC-1:2000 pdf free download
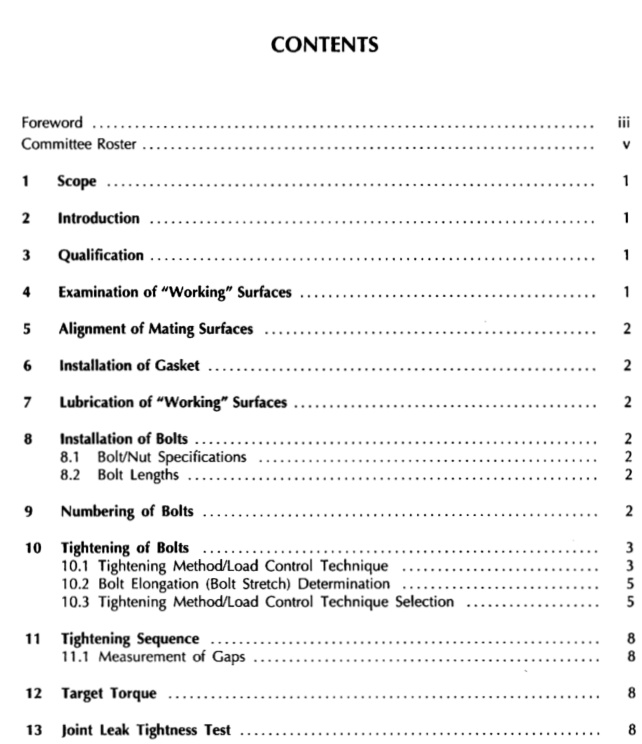