ASME NTB-4:2021 pdf free download Background Information for Addressing Adequacy or Optimization of ASME BPVC Section III, Division 5 Rules for Nonmetallic Core Components
2cODE APPROACH
This section provides the basis for the code and a typical design sequence for a graphite core component.Because there is not a standardized graphite grade for nuclear applications,the code places theresponsibility for determining the design properties of the graphite used on the core designer. The approvedproperties for the selected graphite grade are then determined through material testing and listed in the formof a materials data sheet [4]-[6], which is used to justify the design.
Previous studies [7],[8] determined that variations of the Weibull distribution best describe the graphitereliability curve. HHA–3000 [9] describes how to statistically characterize graphite material based onspecimen test results so that a material reliability curve can be derived. The approach is supported by manyother studies [10]-[17].
To perform a stress-based analysis,the rules derive an equivalent stress state (from a multiaxial stressanalysis) to determine the peak equivalent stress for a component for a given load condition.
In general, parts are designed by comparing calculated stresses to strength limits based on specimen testresults and adequate design margins. But in the case of graphite,fixed design margins do not ensureuniform reliability because of the variability in the material. The stochastic strength (large randomfluctuations from the population mean) and the nonlinear stress-strain response (quasi-brittle) of graphite[18], as well as billet-to-billet variation [19], require that the material be statistically characterized. Thatcharacterization is then used to determine the design margin [20],[21].
The identified modes of failure for graphite are brittle fracture,fatigue, excessive deformation (includingboth elastic instability and irradiation-induced dimensional changes) and environmental effects such asirradiation and chemical attack.
The following are fundamental concepts for the code approach.
lt is possible to allocate probability-of-failure(POF) targets to the graphite parts such that if thetargets are met, the overall functional integrity of the assembly is ensured.
The effects of loads on a part can be calculated and expressed as stress states in the part.Complexstress states can be reduced to an equivalent stress, which is equivalent to uniaxial stresses appliedto test specimens.
The nature of graphite implies that a probabilistic assessment method is better suited to the designof graphite parts than is a deterministic method.
lt is possible to characterize the materials by a statistical treatment of the material specimen testresults to produce a statistical distribution (referred to as the material reliability curve) and generateconfidence intervals to ensure conservatism.
To ensure margin against brittle fracture, for a simple assessment, it is possible to determine stressvalues —based on the POF targets and material test data——so that when the part stresses are lowerthan these limits, adequate reliability of the part is ensured.For a full assessment, it is possible tocalculate expected POF values for a graphite part based on material test data that are directlycomparable to the POF targets and ensure adequate reliability of the part.
Environmental effects such as irradiation and oxidation can be incorporated into the method byconsidering the changes to the input material properties.
To ensure the margin against fatigue fracture, the code requires protection against fatigue failure;but it does not specifically address guidance regarding failure of graphite parts due to fatigue-induced damase for the maior operating cvcles of the reactor(HHA-3144)1221.
The graphite code treats design, service, and test loadings consistently with the rest of the ASME BPVC. The design loadings, defined in HHA-3123.1 through HHA-3123.4 [22], include the distributions of pressure, temperature, fast neutron flux or damage dose rate, and various forces applicable to nonmetallic core components. According to HAB-2142 [23], the design specification defines the design limits (the enveloping case for the design) and service limits according to the designer’s classification with regard to functional performance (Level A); the ability to withstand damage requiring repair (Level B); and the extent to which large deformations in the areas of structural discontinuity (Level C) and gross deformations with consequential loss of dimensional stability and damage requiring repair (Level D) are permitted.
ASME NTB-4:2021 pdf free download
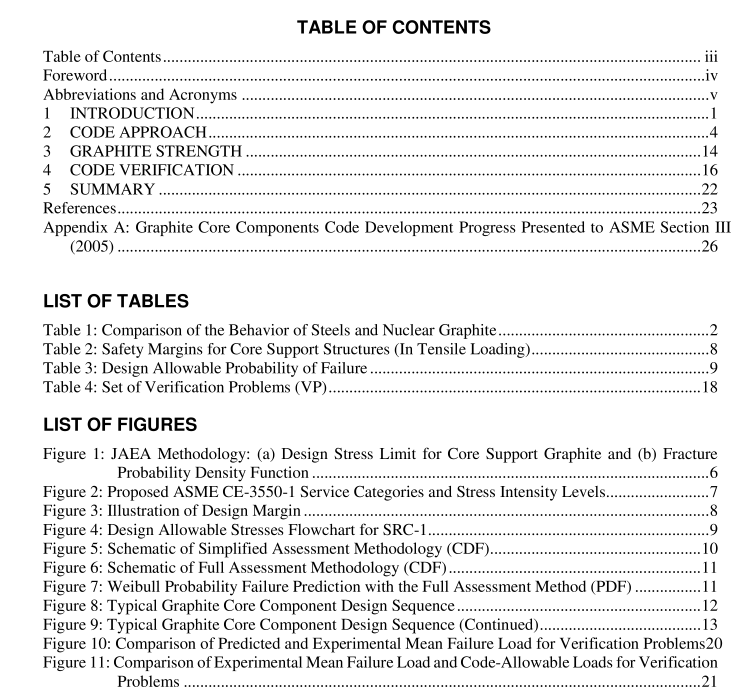