ASME MFC-7:2016 pdf free download Measurement of Gas Flow by Means of Critical Flow Venturis and Critical Flow Nozzles
5APPLICATIONS FOR WHICH THE METHOD IS sUITABLE
Each application should be evaluated to determine whether a CFV is suitable for the conditions and requirements.An important advantage of a CFV is that the flow through it is independent of the downstream pressure as longas the pressure conditions up- and downstream from the CFV lead to critical flow at the throat. The following aresome other considerations:
(a) To calculate flow through a CFV, the only measurements required are the gas composition, and the pressureand temperature upstream of the CFV. These measurements enable the throat conditions to be calculated fromthermodynamic considerations. A low-uncertainty measurement of the throat diameter is also required if Ca valuesare determined using the empirical equations in this Standard. In contrast, if the CFV is flow calibrated, only anominal value of the diameter is necessary (see examples in Nonmandatory Appendix B).CFVs are applicablewhen there is no phase change as the gas accelerates from the inlet to the throat and the flow is not a function ofthe downstream pressure (i.e., the CFV is choked). Care must be taken when using an equation of state at or nearthe dew point of the gas so that correct gas phase properties are determined.Studies have shown that condensationrates in the presence of favorable pressure gradients and rapidly falling temperatures are much slower than thetransit time of the fluid from the CFV entrance to the CFV throat. Therefore, the CFV will operate correctly andyield the correct flow, provided that the calculations for the speed of sound and density at the throat are correct.(b) The velocity in theCFV throat is the maximum possible for the given upstream stagnation conditions; therefore,the sensitivity to installation effects is minimized, except for swirl, which must not exist in the inlet plane of the CFV.(c)Unlike the subsonic differential pressure device, CFV flow is proportional to the inlet stagnation pressureand not to the square root of a measured differential pressure.
(d) The maximum flow range that can be obtained for a given CFV is limited to the range of inlet pressures thatare available above the inlet pressure at which the flow becomes critical.
(e) The most common applications for CFVs are the calibration of other meters (working or reference standards)and verification or comparison of primary flow standards (check or transfer standards) in flow control applicationsand in product testing.
6STANDARD CRITICAL FLOw VENTURIS6.1 General Requirements
6.1.1 Discharge Coefficient.The discharge coefficient, Ca, for a CFV may be obtained by either the empiricalmethod (using empirical or theoretical equations of Caversus Reynolds number) or the calibration method (calibra-tion of the particular CFV in a flow laboratory). When using empirical Ca values, the specifications for size, shape,and surface conditions are pertinent to obtaining the performance specified in this Standard. In these cases theCFV should be inspected to determine conformance to construction specifications of this Standard. In the case oflaboratory-determined C values, compliance with the following construction specifications is less pertinent. Whenit is not practical to manufacture CFVs to the surface finish and curvature specifications herein, CFV performancemust be demonstrated through calibration against a flow reference.
6.1.2 Materials.CFVs should be manufactured from material suitable for the intended application, such asthe following:
(a)The material should be capable of being finished to the surface condition specified in this Standard. omematerials are unsuitable because of pits, voids, and other nonhomogeneities.
(b) The material, together with any surface treatment used, should not be subject to corosion in the intendedservice. Experience has shown that 300 series stainless steel is often a suitable material.
ASME MFC-7:2016 pdf free download
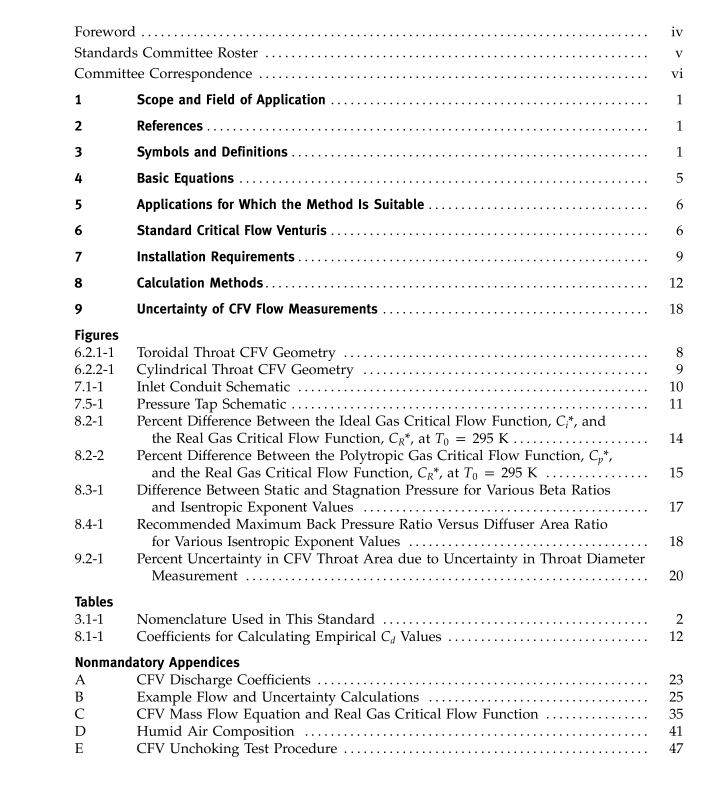