ASME MFC-16:2007 pdf free download Measurement of Liquid Flow in Closed Conduits With Electromagnetic Flowmeters
6.2 Effects of Process Properties and Flow Profiles
6.2.1 Sizing Based on Accuracy and velocity.Thelinearity of industrial electromagnetic flowmeters maybe affected by the distorted velocity profile that is pres-ent at low pipe Reynolds numbers.The effect should beincluded in the manufacturer’s specifications.
6.2.2 Velocity Profile Effect.Pipe fittings (such asbends, valves, reducers, etc.) located upstream or down-stream of the flowmeter may cause distortions in veloc-ity profile. The distorted flow patterns may influencethe performance of the meter (see para.6.4.1.1).
6.2.3 Slippage. When solids move at velocities dif-ferent from the flowing liquid, slippage occurs. In verti-cal installations with an upward flow direction, settlingsolids can cause the electromagnetic flowmeter to under-register or, in extreme cases, appear as zero or reverseflow.Conversely, in vertical installations with a nor-mally downward flow direction,settling solids can causethe electromagnetic flowmeter to over-register. Consultthe manufacturer for all slurry applications.
6.2.4 Triboelectric Effect.The triboelectric effect(static electricity) is an electrical phenomenon wherematerials become electrically charged due to the effectsof friction.The triboelectric effect in electromagneticflowmeters occurs when certain materials (typicallynonconducting, such as silicates, petroleum-based liq-uids or solids, etc.) deposit an electrical charge (eitherpositive or negative)on the electrodes of the meter.These charges can either introduce errors or electricalnoise, or both. Consult the manufacturer when applica-tions include nonconductive particles.
6.3 Flowmeter Primary – Sizing considerations
6.3.1 General Considerations.Many electromag-netic flowmeters have a relatively wide turndown, so itis generally feasible to select a flowmeter primary of thesame size as the adjacent piping.However, it should benoted that liquid velocity range, upstream and down-stream piping and other flow considerations should bethe basis in choosing the meter diameter for a givenapplication. Consideration must be given to both themaximum and minimum flow rates if the end-userrequires the meter to perform as specified by the manu-facturer.
6.3.1.1 Accuracy.Manufacturers must specify themeter accuracy over the liquid velocity range of theflowmeter primary. If a low velocity condition exists, itmay be desirable to size the meter at less than the nomi-nal process piping size to increase the velocity (seepara.6.4.2.4).
6.3.1.2 Pipe Mismatch. Nonuniform entrance andexit conditions, such as inlet-outlet and liner internaldiameter (ID) mismatches may cause changes in thevelocity flow profile, which may cause additional flow measurement errors.Of particular concern is the “jeteffect” that occurs when the pipe immediately precedingand following the flowmeter primary has an ID lessthan that of the flowmeter primary (see para.6.4.2.4).
6.3.1.3 Abrasive Slurries.Excessive wear shouldbe a consideration for increasing the pipe diameter inthe measuring section of the piping (i.e., the flowmetersensor, and the preceding and following piping) toreduce the liquid flow velocity.
NOTE: Excessive liner wear can be caused by an asymmetricalflow profile (see para.6.2.2), improper liner material selection (seepara. 6.5.2), or horizontal installation of the flovwmeter primary.In particular, the upstream edge of the liner may besubject to wear from abrasive slurries. To minimize thisupstream edge wear, it is beneficial to match the internaldiameter of the flowmeter primary and the nearupstream piping. Metal protection rings can also beinstalled to reduce the wear on the edge of the liner.Consult the manufacturer for guidance regardingmaterials of construction and installation experience forapplications with abrasive slurries.
6.3.1.4 Fast-Settling Slurries. Velocities must besufficient to keep slurry solids in suspension when themeter is mounted horizontally.Furthermore, if solidsare prone to settle during no-flow conditions, there mustbe sufficient velocity to flush the settled materials fromthe flowmeter primary at startup (see para.6.4.1.3)-6.3.2 Special Process Considerations.There may besituations where it is desirable to size the flowmeter atother than the pipe size. When this is the case, the processliquid properties and velocity range of the flowmetermust be considered.As a matter of practice, applicationsutilizing small meters [12 mm (/ in.) and less] are moresensitive to pipe mismatch effects than larger metersand should be given special consideration.
6.4 Flowmeter Primary – Location,Installation, and
Maintenance
6.4.1 Flowmeter Primary Location and Orientation.Generally, there are no restrictions on flowmeter primaryorientation (horizontal, vertical, or inclined). However,it is essential that the flowmeter primary be full of theprocess liquid to ensure proper performance.
The performance of electromagnetic flowmeters maybe influenced by the location and orientation of theflowmeter primary with respect to the process piping.Consequently, paras.6.4.1.1 through 6.4.1.5 should beconsidered.
ASME MFC-16:2007 pdf free download
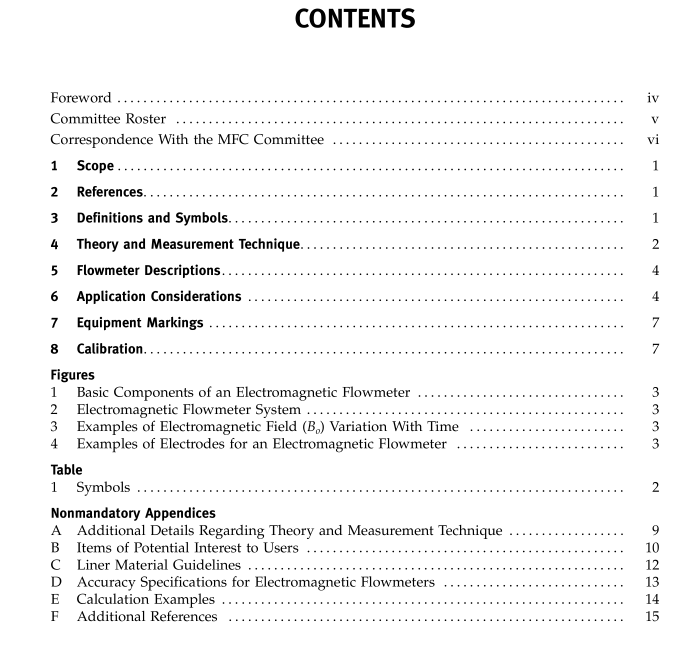