ASME B18.29.1:2010 pdf free download Helical Coil Screw Thread Inserts— Free Running and Screw Locking (Inch Series)
3.4 Configuration and Dimensions
Insert configurations shall be in accordance withFig. 1, and dimensions shall be in accordance withTables 3 and 4.
3.4.1 Nominal Length. Each nominal insert size isstandardized in five lengths which are multiples of theinsert’s nominal diameter. These are 1,11/5,2,21/5, and3 times nominal diameter.
Each nominal length is the minimum through-holelength (material thickness),without countersink,intowhich that insert can be installed. The nominal insertlength is a reference value and cannot be measured.
3.4.2 Assembled Length. Actual assembled lengthof the insert equals nominal length minus 1% pitch tominus 3/4 pitch,with insert installed in a basic STIthreaded hole. It cannot be measured in the insert’sfree state.
4INSPECTION AND QUALITY ASSURANCE
Unless otherwise specified by the purchaser, theinspection of inserts shall be in accordance withASME B18.18.2 with inspection level 3 for a 15-cycletorque test as described in para.4.2.3.
4.1 Inspection (Nondestructive)
4.1.1 Examination of the Product. Inserts shall bevisually examined for conformance with drawings andworkmanship requirements in accordance withASME B18.18.2.
4.1.2 Threads. The inserts,when assembled in STr
conforming tooAorming to Table1,shall forema tinsTrClass 2B except for the locking feature of screw-locking inserts.The assembled insert,both types,shall acceptand function with parts having external UNJ threadsper SAE AS8879.
NOTE: Accuracy of the finished thread,when the insert isinstalled, is dependent upon the accuracy of the tapped hole. ifthe finished tapped hole gages satisfactorily, the installed insert
will be within the thread tolerance when the insert meets therequirements of the Standard. lt is, therefore, not necessary to gagethe installed insert.After the insert is installed, the Go thread pluggage may not enfer freely because the insert may not have beenfully seated in the tapped hole.However, the insert should becomeseated after a bolt or ‘screw is installed and tightened.
4.1.3 Tang Removal Notch. The tang removal notchshall be located as shown in Fig. 1 and shall be of suchdepth that the part may be installed without failureof the tang, and that the tang may be removed, afterassembly, without affecting the function of the installedinsert.
4.2 Screw-Locking Insert Self-Locking Torque (Destructive) Testing The screw-locking insert, when assembled in threaded holes conforming to Table 1 and tested in accordance with the following paragraphs, shall provide a frictional lock to retain the bolt threads within the torque limits specified in Table 5.
4.2.1 Torque Test Bolts. Assembled screw-locking inserts shall be torque-tested with bolts in accordance with ASME B1.1, cadmium plated, or have other coating with a similar coefficient of friction and a hardness of 36 HRC to 44 HRC. The bolts selected for this test shall be of sufficient length so the thread run out does not enter the insert and that a minimum of one full thread extends past the end of the insert when the bolt is fully seated. Acceptability of bolt threads shall be determined based on System 22 of ASME B1.3 (see Note below).
NOTE: Until a replacement for cadmium plating on the torque test bolts (as specified in para. 4.2.1) is found, and test data com- pleted, an alternate coating, lubricant, or both, can be used to perform the torque test (values may be different from those obtained using cad plated screws) based on agreement between the customer and the insert supplier.
4.2.2 Torque Test Block. The insert to be tested shall be installed in a Class 3B threaded hole conforming to Table 1 in a test block made from 2024-T4 (SAE AMS4120, ASTM B 209-02) aluminum alloy. After installation, the tang shall be removed. The surface of the test block from which the insert is assembled shall be marked to indicate the radial location where the assembled insert begins.
4.2.3 Torque Test Method. The torque test shall con- sist of a 15-cycle, room temperature test. A new bolt or screw and a new tapped hole shall be used for each complete 15-cycle test. Bolts must assemble freely, with the fingers, up to the locking coil or coils. The bolt shall be engaged and disengaged from the assembled insert for 15 full installation and removal cycles. The test shall be run at less than 40 rpm to yield a dependable measure of torque and avoid heating of the bolt. A bolt shall be considered fully installed when three threads extend past the end of the locking coils of the insert. The removal cycle shall be considered complete when the locking coils are disengaged.
ASME B18.29.1:2010 pdf free download
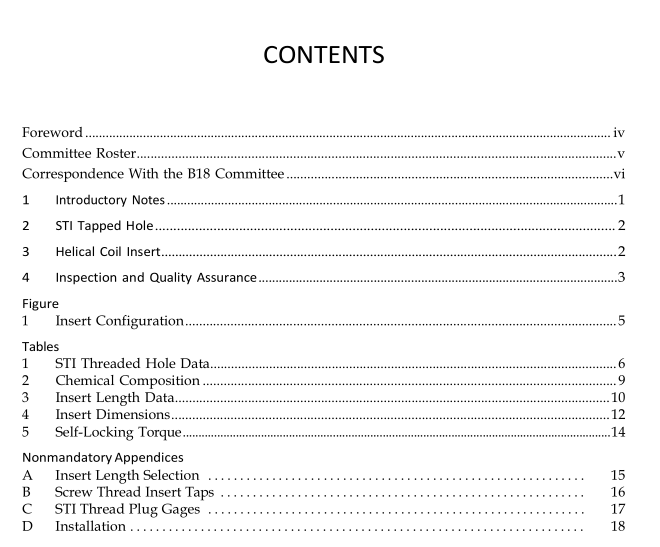