ASME B18.18:2011 pdf free download Quality Assurance for Fasteners
This Standard places a C=0expectation on the sampleplans shown herein. However it should be recognizedthat zero nonconformities (C=0) in a sampling does notnecessarily mean that the population is entirely free ofdefects.
Statistical process control and other variation low-ering measures can significantly reduce the number ofdefects in the population that may be produced, but itshould be noted that statistical indices only imply thequality level produced, and improperly applied statisti-cal treatments will imply the presence of defects thatare not present,or miss some deficiencies altogether.The closest that one can approach zero defects in apopulation is through 100% part per part examination,but again caution must be exercised. The goal of zerohere can be intractable.The complexity of resourcesrequired, the limitations of the available equipment foreach verified characteristic, the stringency of controlsrequired will only be able to demonstrate quality on aparts per million (PPM) basis, and not necessarily anyassurance of zero deficiencies.
2.2 In-Process Inspection
2.2.1 Fabricating operations.General inspectionprocedures shall be established on the basis of engi-neering and manufacturing experience with regard tothe effort of setup,tooling, operator,machine setup,and operation on each characteristic at each processingstation. The minimum in-process requirements at eachmachine or processing station shall be as follows:(a) Five pieces shall be visually examined for grossdefects and surface discontinuities as required by theapplicable standards. Three pieces shall be verified forpart characteristics imparted to it by that machine orprocessing station in accordance with Table 1 at thefollowing times:
(1) at the start of each production run(2) at the start of each new shift
(3) when a tool is changed or when an adjustmentin machine setup is made
( 4) at the completion of each manufacturingoperation
NOTE:When tungsten carbide dies are used, it is only necessaryto verify a single piece for formed dimensions.
(b) During the production run, on a frequency of notless than one part per every 2 hr, parts shall be inspectedfor all designated part characteristics imparted to it bythat machine or processing station in accordance withTable 1.
2.2.2 Heat Treatment.All heat treating processesand heat treatment equipment shall be regularly moni-tored to ensure process control and proper functioningof equipment.
2.2.3 Finishing Operations.All plating, coating,andpost lubrication processes and equipment shall be regu-larly monitored to ensure process control and properfunctioning of equipment per applicable standards andspecifications.
NOTE: Records of in-process inspections are not required for anycategory. If process records are maintained for Category 3 products,the lower final inspection sample sizes shown in Table 2 may beused instead of the sample sizes indicated in Table 3.
2.3 Final Inspection
Every lot of fasteners shall be subjected to a finalinspection in accordance with the specified final inspec-tion category.The final inspection is intended to verifylot identification and to inspect designated characteris-tics for conformance to related standards, specifications,and engineering drawings. Final inspection of any char-acteristic may be conducted at any point after whichthat characteristic will not be altered. Records of finalinspection shall be maintained in accordance withpara. 2.6.
2.4 Acceptance and Rejection
2.4.1 Raw Material. All raw material (rod, wire,bar,or sheet) shall meet the applicable requirements.Nonconforming raw materials shall not be used for theproduction of fasteners and shall be quarantined untildisposition.
2.4.2 Manufactured Products.All parts shall con-form to the applicable requirements during in-processinspection at all fabricating, heat treatment, or finishingoperations. When nonconforming parts are found, allparts produced since the last inspection of the character-istic(s) found nonconforming shall be removed from fur-ther processing, quarantined, and held for disposition.
2.4.3 Sampling Acceptance Criterion.The accept-ance criterion for final inspection is zero discrepancies(C=0) for all inspections.
2.5Disposition of Nonconforming Materials or PartsRecords of disposition shall be maintained in accor-dance with para. 2.6.
ASME B18.18:2011 pdf free download
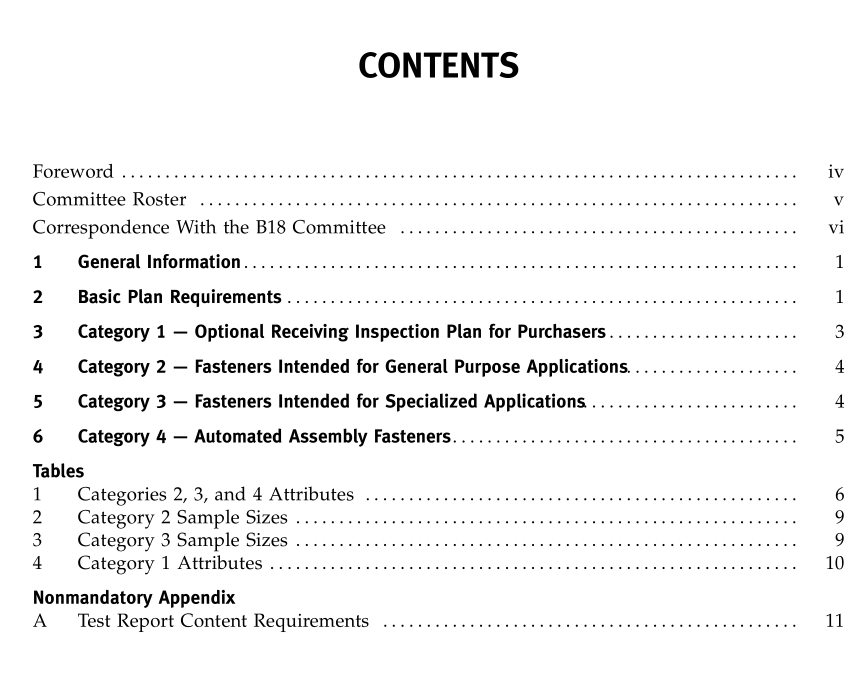