ASME B18.16M:2004 pdf free download Prevailing- Torque Type Steel Metric Hex Nuts and Hex Flange Nuts
ISO 7044, Prevailing torque type all-metal hexagon nutswith flange — Product grades A and B
ISO 7719,Prevailing torque type all-metal hexagon nuts,style 1 — Property classes 5,8 and 10
Iso 7720,Prevailing torque type all-metal hexagon nuts,style 2 — Property class 9
Publisher: International Organization for Standardiza-tion (ISO), 1 rue de Varembe,Case Postale 56,CH-1211,Geneve 20, Switzerland/Suisse
SAE J121M.Decarburization in Hardened and Tem-pered Metric Threaded Fasteners
Publisher: Society of Automotive Engineers (SAE),400Commonwealth Drive, Warrendale,PA 15096-0001
4TERMINOLOGY
For definitions of terms relating to fasteners or com-ponent features thereof used in this Standard, refer toASME B18.12.
Unless otherwise noted, all references to nuts in thisStandard mean prevailing-torque hex nuts and hex flange nuts.
5 DIMENSIONS
Unless otherwise stated, all dimensions in this Stan-
dard are in millimeters (mm),and apolv before an nlat-ing or coating. When a plating or coating is specified,the finished product dimensions shall be as agreed uponbetween supplier and purchaser.
Symbols specifying geometric characteristics are inaccord with ASME Y14.5M.
6NUT DESIGNS AND PROPERTY CLASSESThere are three basic designs for prevailing-torquenuts.
(all-metal, one-piece construction nuts which de-rive their prevailing-torque characteristics from con-trolled distortion of the nut thread and/or body(b)metal nuts which derive their prevailing-torquecharacteristics from the addition or fusion of a non-metallic insert, plug, or patch in their threads top insert, two-piece construction nuts which de-rive their prevailing-torque characteristics from an in-sert, usuaily a full ring of nonmetallic material, locatedand retained in the nut at its top surface
The two nut designs defined in paras. 6(a) and (b)have the same dimensional requirements and are des-ignated “all-metal type” in Tables 1 and 2. Nut design6(c) is designated “top insert type” in Tables 1 and 2.
7 wIDTH ACROSS FLATS
The width across flats shall be the distance, measuredperpendicular to the axis of the nut, between two op-posite wrenching flats.The maximum width across flatsmay be exceeded by 0.05 mm to allow for nut defor-mation caused by introduction of the prevailing-torquefeature.The width across flats and width across cornersmay be less than the specified minimum in the deformedportion of the nut containing the prevailing-torque fea-ture.
At maximum material condition the axis of the hexa-gon shall be located at true position with respect to theaxis of the thread pitch diameter within a tolerance zonehaving a diameter equivalent to 4% of the maximumwidth across flats.
8THICKNESS
The nut thickness shall be the overall distance, meas-ured parallel to the axis of the nut, from the top of thenut to the bearing surface of hex nuts, and to the planeof the bearing circle diameter of hex flange nuts. Raisedidentification markings, if present, shall be excluded.9WRENCHING HEIGHT
The wrenching height is the distance, measured at acorner of the hex, from the bearing surface of hex nuts,and from the junction of the hex portion with the flangeof hex flange nuts to the last plane of full formed hex,i.e., the plane perpendicular to the nut axis that is clos-est to the top of the nut and at which the width acrosscorners is within its specified limits.Wrenching heightfor hex nuts is dimension M in Table 1,and is subjectto measurement. Wrenching height for hex flange nutsis dimension Ta in Table 2 and is controlled by the gag-ing requirement specified in para.10.
10GAGING OF HEX PORTION OF
HEX FLANGE NUTs
The nut shall be gaged using two plain ring gages,Aand B, to demonstrate the coincidental acceptability ofhex height, wrenching height, and width across corners.(See figure above Table 2.) Gage A shall be placed overthe hex and shall seat on the flange.Gage B shall beplaced on the top of the nut normal to the nut axis.Thetwo gages shall not be in contact.
NOTE: The minimum inside diameter of Gage A equals the max-imum width across corners; the maximum inside diameter of GageB equals the minimum width across corners minus 0.01 mm; themaximum thickness of Gage A was computed to be equal to orgreater than the wrenching height necessary to provide sufficientdriveability to develop two times the torsional strength of theproperly mated, externally threaded component.
ASME B18.16M:2004 pdf free download
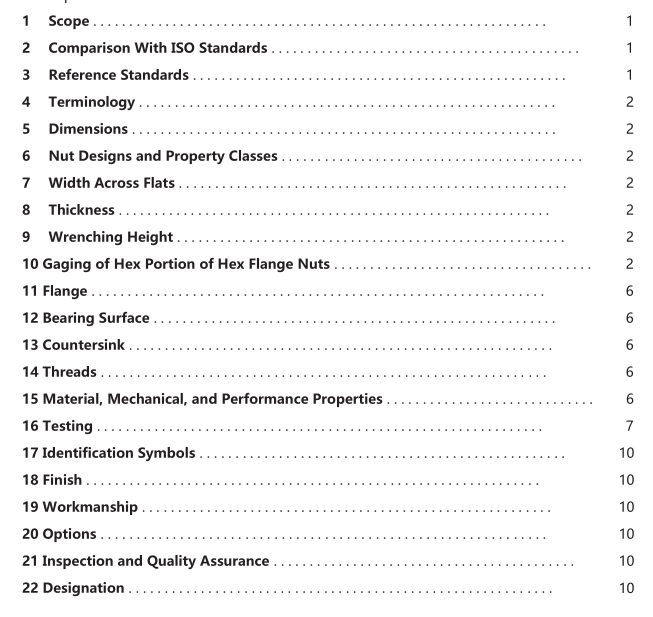