ASME B16.44:2002 pdf free download MANUALLYOPERATED METALLIC GAS VALVES FOR USEIN ABOVEGROUND PIPING SYSTEMS UP TO 5 PSI
1 sCOPE1.1 General
This Standard applies to new valve construction andcovers quarter turn manually operated metallic valvesin sizes NPS 41/4 and tubing sizes 11/4 O.D. These valvesare intended for indoor installation as gas shutoff valveswhen installed in aboveground fuel gas piping down-stream of the gas meter outlet and upstream of the inletconnection to a gas appliance.The valves covered bythis Standard are intended for service at temperaturesbetween 32°F(0°C) and 125°F(52°C) at pressure ratingsnot to exceed 5 psi (0.34 bar).When so designated by themanufacturer, these valves may be installed for serviceoutdoors and / or at temperatures below 32°F(O°C) and/or above 125°F (52°C).
1.2 Applicability
This Standard sets requirements, including qualifica-tion requirements, for metallic gas valves for use in gaspiping systems. Details of design, materials, and testingin addition to those stated in this Standard that arenecessary to meet the qualification and production test-ing requirements of this Standard remain the responsi-bility of the manufacturer. A valve used under a codejurisdiction or governmental regulation is subject to anylimitation of such code regulations.
1.3 Limitations
This Standard does not apply to manually operatedgas valves that are an integral part of a gas appliance.Manually operated gas valves intended for use in aparticular appliance are covered in the AmericanNational Standard/Canadian Gas Association Standardfor Manually Operated Gas Valves for Appliances,Appliance Connector Valves, and Hose End valves,ANSI Z21.15/CGA 9.1.
1.4 Convention
For the purpose of determining conformance withthis Standard , the convention for fixing significant digitswhere limits, maximum and minimum values, are speci-fied by “rounding off as defined in ASTM Practice E29.This requires that an observed or calculated value shall be rounded off to the nearest unit in the last right-hand digit used for expressing the limit. Decimal valuesand tolerances do not imply a particular method of mea-surement.
1.5 Quality Systems
Requirements relating to the product manufacturer’sQuality System Programs are described in Nonmanda-tory Annex A.
1.6 Units
The values stated in either inch units or metric unitsare to be regarded separately as standard.The valuesstated in each system are not exact equivalents; therefore,each system must be used independently of the other.Combining values from the two systems may result innon-conformance with the standard.
All pressures,unless otherwise specified, are gaugepressures.
GENERAL CONSTRUCTION AND ASSEMBLY2.1 General
Each valve at the time of manufacture shall be capableof meeting the requirements set forth in this Standard.The workmanship employed in the manufacture andassembly of each valve shall provide for the specifiedgas tightness, reliability of performance, freedom frominjurious imperfections, and defects as specified herein.2.2 End connections
The valve body shall be provided with wrench flatsat ends with tapered pipe threads.
2.3 Pipe and Tubing Connections
2.3.1 Taper Pipe Threads. Taper pipe threads, whenprovided, shall be in accordance with ASME B1.20.1.2.3.2 Flare Tubing Connection. Valves with an inletand / or outlet for 3/, 1%, or 5O.D. tube shall be in accor-dance with the flare fitting dimensions shown in Table1.Other flare sizes shall be made per manufacturer ‘sstandards.
2.4 Operating Head
The operating head of the valve shall be a lever, tee,flat, or square head type. Separately attached handles,if provided, shall be securely attached to the valve by the use of threaded fasteners, retaining pins, or their equivalent. \2.5 Operation The valve shall require 1 ⁄ 4 turn from the full closed position to the full open position, or from the full open position to the full closed position. \2.6 Position Indication The valve shall be so constructed that the operator can visually determine that the valve is in the open or closed position. When the valve is in the closed position, the operating lever or flow indicator shall be perpendic- ular to the longitudinal axis of the valve.
ASME B16.44:2002 pdf free download
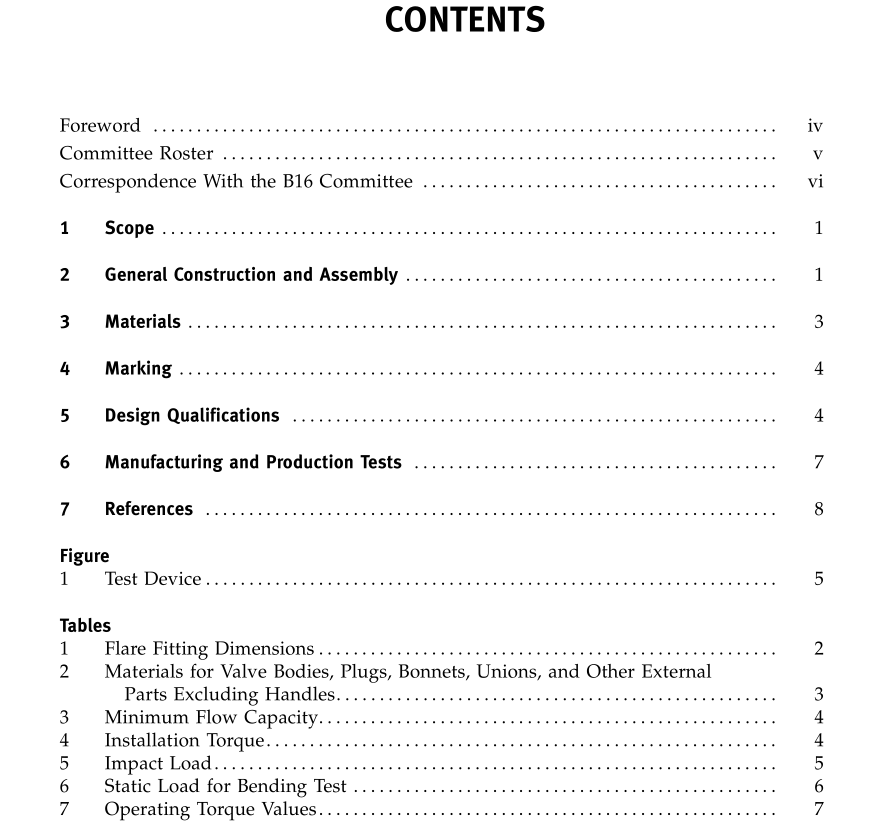