ASME B16.40:2008 pdf free download Manually Operated Thermoplastic Gas Shutoffs and Valves in Gas Distribution Systems
The full test differential pressure shall be applied across the downstream seat if there is more than one seat. The test fluid shall be air or other gas and there shall be no visible leakage (no breaking away or buildup of bubbles) at the downstream seat as measured by the water over air or a leak detection solution method. If immersion is used, the depth from the water surface shall be no more than 12 in. (300 mm). Other means of leak detection may be used, provided they can be shown to be equivalent in leak- detection sensitivity. The seat test shall be conducted at a temperature of 73 ± 15°F (23 ± 8°C). The seat test’s fixturing shall not restrain the valve against any mode of failure or leakage. The minimum duration of each portion of the test shall be as shown in Table 2.
3.3 Qualification Testing
3.3.1 Operational Test. It shall be demonstrated that each nominal size of each valve design is capable of successfully passing the seat leakage tests of para. 3.2.2, after having completed ten fully opened/fully closed cycles at 73 ± 15°F (23 ± 8°C). The valve shall be pressurized with air or other gas to the design pressure at one port with the other port open to atmosphere before opening on each cycle. At the start of each cycle, the operating torque shall be measured and shall not exceed those in Table 3 for −20°F (−29°C).
3.3.2 Temperature Resistance. It shall be dem- onstrated that each nominal size of valve of each valve design is capable of being operated at temperatures of −20 ± 5°F (−29 ± 3°C) and 100 ± 5°F (38 ± 3°C) without visible leakage to atmosphere and without affecting the internal seat-sealing performance of the valve. The method of test is as follows. A closed valve shall be cooled to a temperature of −20 ± 5°F (−29 ± 3°C) and held there for 18 hr minimum. The valve shall then be pressurized with air or gas to a differential pressure across the seat equal to the design pressure.
4 The valve shall then be opened against the applied- differential pressure, using a torque less than or equal to that of Table 3 at the −20°F (−29°C) values and then closed (no differential pressure across the seat required). The valve shall then be tested to meet the requirements of para. 3.3.2 while at −20°F (−29°C), except nonfreezing leak-detection agents shall be used. The valve shall then be heated to a temperature of 100 ± 5°F (38 ± 3°C) and held there for 18 hr minimum. The closed valve shall then be pressurized with air or other gas to a differential pressure across the seat equal to the design pressure. The valve shall then be opened against the applied-differential pressure using a torque equal to that of Table 3 100°F (38°C) values and then closed (no differential pressure across the seat required). The valve shall then be tested to and meet the require- ments of para. 3.3.2, while at 100°F (38°C).
3.3.3 Sustained-Pressure Test. Each basic valve design shall be subjected to sustained-pressure tests to determine the effects of 1,000 hr pressure loading. Each variation in material, size, or configuration of molded pressure-containing parts shall constitute a different basic design. Where minor design variations are pro- duced by differences in machining of valve-end connec- tions to match pipe of different size or SDR rating, only valves with the lowest SDR rating (corresponding to the SDR equivalent rating of the valve) and in the largest size need to be tested.
(a) Pressure-Boundary Tests. Six samples of each basic valve design shall be connected at both ends to thermoplastic pipe of appropriate wall thickness of a length of at least five times its outside diameter or 20 in. (510 mm), whichever is less. These assemblies shall be subjected to a sustained-pressure test for 1,000 hr (valves in open position), using water at 73 ± 4°F (23 ± 2°C) as described in the Sustained-Pressure Test section of ASTM D 2513. The SDR equivalent for the valve shall be used in determining the test pressure from Table 4A. Failure of two of the six samples tested shall constitute failure in the test. Failure of one of the six samples tested is cause for retest of six additional samples. Failure of one of the six samples in retest shall constitute failure in the test. Evidence of failure shall be as defined in ASTM D 1598 applied to a valve test sample. An additional six samples of each basic valve design shall also be subjected to a similar sustained-pressure test for 1,000 hr, using water at a temperature of 100 ± 4°F (38 ± 2°C) and an appropriate test pressure from Table 4B. Criteria for failure shall be the same as described above for the 73°F (23°C) test.
ASME B16.40:2008 pdf free download
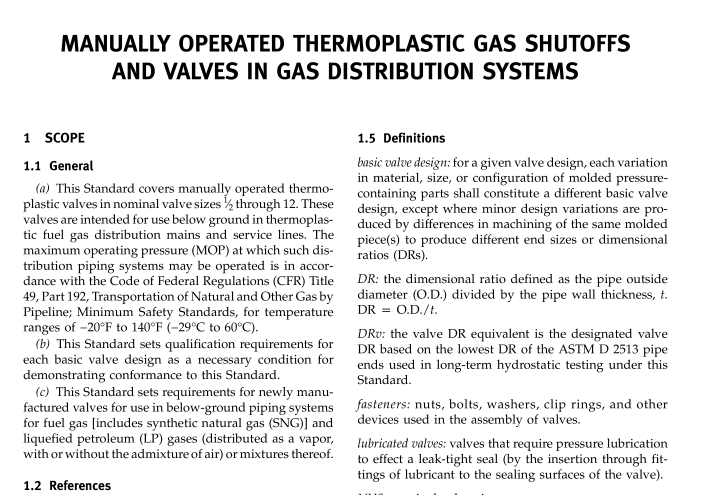