ASME B16.38:2007 pdf free download Large Metallic Valves for Gas Distribution Manually Operated, NPS 2 1 / 2 (DN 65) to NPS 12 (DN 300), 125 psig (8.6 bar) Maximum
2.3 Configuration
2.3.1 Closure Indication
2.3.1.1 Valves designed for one-quarter turn operation shall be designed to visually show the open and closed position of the valve. A rectangular stem head or a position indicator shall indicate the closed position of the valve port when the longitudinal axis of the stem head or indicator is perpendicular to the axis of the connecting pipe. If a separate indicator is employed, it shall be designed such that it cannot be assembled to incorrectly indicate the position of the valve.
2.3.1.2 Valves shall close by clockwise stem rota- tion unless otherwise specified by the purchaser or by the reference standard in para. 2.1.2. The direction for closing shall be indicated.
2.3.2 Valve Ends. Valve ends shall conform to the following standards where applicable:
(a) for threaded valve ends, ANSI/ASME B1.20.1
(b) for flanged gray cast iron valve ends, ASME B16.1
(c) for flanged ductile cast iron valve ends, ASME B16.42
(d) for flanged steel valve ends, ASME B16.5
(e) for flanged, butt-welding, and socket-welding valve ends, ASME B16.34 2.3.3 Dimensions. Face-to-face and end-to-end dimensions of valves (other than ball, butterfly, or dia- phragm valves) with flanged ends or butt-welding ends shall conform to the dimensions contained inMSS SP-72. Face-to-face dimensions for butterfly valves shall be in accordance with dimensions contained in MSS SP-67. End-to-end dimensions of threaded end valves shall be in accordance with the manufacturer’s standard dimensions.
2.4 Marking Each valve, in addition to the markings required by the applicable valve standard of para. 2.1.2, shall bear the marking “B16.38” or “B16.38T” if tamperproof fea- tures are included according to para. 2.2. Alternative to the latter, the marking “T” may be shown on the operating head or stem.
2.5 Injection Sealant A valve that utilizes injection of sealant through a fitting that leads to the sealing surfaces shall be capable of having sealant injected in both the full-open and -closed positions at an inlet pressure of125 psig (8.6 bar).
2.6 Pressure-Containing Materials Materials for valve bodies, plugs, bonnets, unions, and other pressure-containing parts shall be in accor- dance with the applicable standards of para. 2.1.2. 2
2.7 Gas Resistance All materials, including lubricants and sealants, shall be resistant to deterioration when exposed to fuel gases such as listed in para. 1.2.
2.8 Temperature Resistance The materials used for valve bodies, plugs, bonnets, unions, and other pressure-containing parts, excluding handles, shall have a solidus temperature in excess of 600°F (427°C).
2.9 Elastomer Components
2.9.1 Air Aging Tests. Elastomer parts that are exposed to fuel gas shall be made of materials that [fol- lowing 70-hr air aging at 212°F (100°C) in accordance with ASTM D 573] meet elongation, tensile, and hard- ness property requirements as specified in paras. 2.9.1.1 and 2.9.1.2.
2.9.1.1 Tensile tests shall be conducted in accordance with ASTM D 412. Three dumbbells shall be air aged 70 hr at 212°F (100°C) in accordance with ASTM D 573. The dumbbells shall have a thickness of 0.08 in. ± 0.008 in. (2 mm ± 0.2 mm). The average of the three individual tests for the aged dumbbells shall exceed 60% retention of ultimate elongation and 60% retention of tensile strength at break. The average of the three individual tests for the nonaged dumbbells shall be the basis for the percent calculation.
2.9.1.2 Hardness tests shall be conducted using specimens in accordance with ASTM D 395, Type 2. Three specimens shall be air aged 70 hr at 212°F (100°C) in accordance with ASTM D 573. The average of the three individual tests for the aged specimens shall not show a hardness change of more than ±10 Shore A hardness points relative to the average hardness of the non- aged specimens.
2.9.2 Swell Tests. Elastomer parts that are exposed to fuel gas shall be made from materials that after 70-hr exposure to N-hexane at 74°F (23°C), in accordance with ASTM D 471, meet the volume change, elongation, and tensile property requirements as specified in paras. 2.9.2.1 and 2.9.2.2.
2.9.2.1 Volume change tests shall be conducted using six specimens in accordance with ASTM D 471, Section 8. Three specimens shall be exposed for 70 hr at 74°F(23°C) inN-hexane inaccordance withASTMD 471. The average of the three N-hexane tests shall not show an increase in volume of more than 1%. The average of the three tests for nonaged specimens shall be the basis for the percent retention calculation.
ASME B16.38:2007 pdf free download
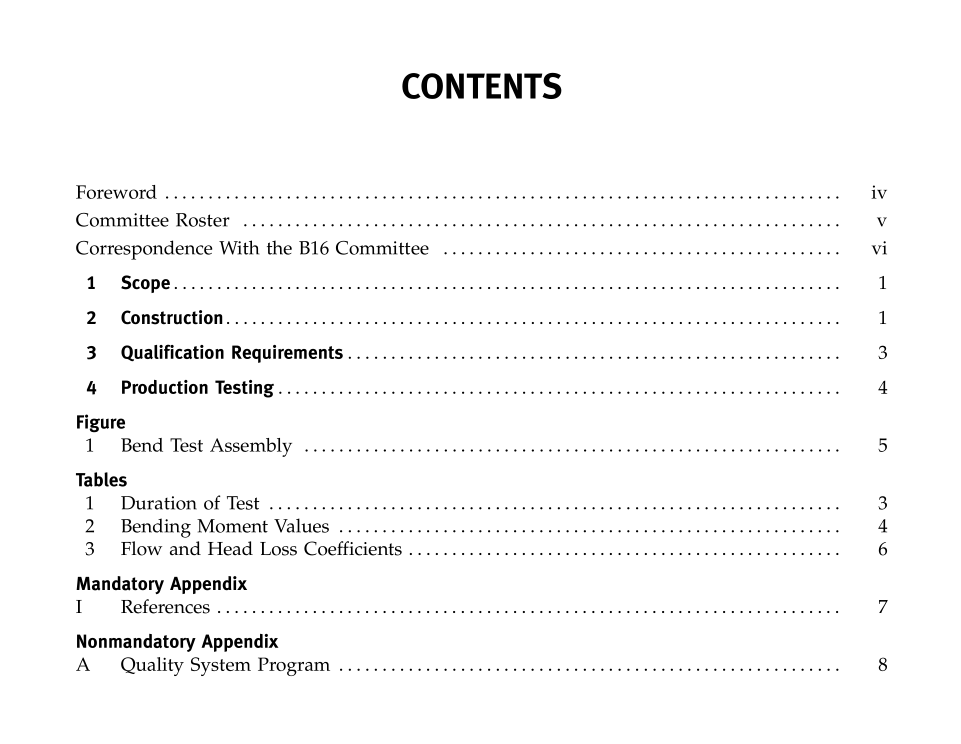