ASME B107.15:2002 pdf free download FLAT TIP SCREWDRIVERS
5 REQUIREMENTS
5.1 General Requirements The ilustrations herein are descriptive, not restrictive, and shall not preclude designs otherwise in accordance with the requirements of this Standard.
5.1.1 Type L, Flat tip straight sided cabinet screw- drivers are for driving and removing slotted screws. The entire length of the blade shall be capable of entering a round hole no larger than the maximum allowable tip width dimension plus 0.031 in. (0.79 mm). Figure 2 ilustrates typical appearances for Class 1 plain and Class 4 pocket with the pocket clip optional.
Screwdrivers shall conform to the dimensional and performance characteristics specified in Tables 1 and 2.
5.1.2 Type I. Flat tip flared sided general purpose screwdrivers are for driving and removing slotted screws. Figure 2 illustrates typical appearances for Class 1 plain, Class 2 bolster, and Class 3 stubby. Screwdrivers shall conform to the dimensional and performance characteristics specified in Tables 1 and 2.
5.2 Materials The materials used in the manufacture of a screw- driver shall be such as to produce products conforming to the performance requirements specified herein.
5.3 Markings Each screwdriver shall be marked in a legible manner with the manufacturer’s name or identification, country of manufacture, and product number. The mcthod of marking shall be such that it will remain legible under normal usage over an extended period,
5.4 Blade
5.4.1 General Requirements. Blades made of steel shall be properly heat treated to meet the perform- ance specified herein. The blade shall be held securely in the handle. The blade shall be essentially free from scale,seams,laps,and cracks,which may adversclyaffect durability or serviceability of the tool.
5.4.2Finish. The blade shall be treated in a mannerto resist rust or corrosion.There shall be no evidenceof pecling or chipping of any coating whcre applicable.
5.4.3 Hardness. The tip portion of the screwdriversor the entire blade shall be hardened to not less than48 HRC (para. 6.2).
5.4.4 Symmetry.See Fig. 3.The tip width shallbe perpendicular to the shank axis within 2 deg. Thetip thickness shall be perpendicular to the shank axiswithin 6 dcg.Taper at the tip shall be centered within5 deg of the shank axis.
5.5 HANDLE
5.5.1 General Requirements.The handle shallbe of a material capable of withstanding the applicabletest requirements as specified herein.The handle shallbe suitably finished to provide a comfortable grip. Thehandle shall be free from rough edges, sharp corners,or tool marks that affcct comfort whilc using the tool.
5.5.2 Cushion Grip.When specified, the handleshall be furnished with a cushion grip.and the screw-driver shall typically resemble that shown in Fig.4The grip material shall be capable of mceting the tests of paras.6.7 and 6.8.The durometer hardness shallbe a maximum of Shore A 75 (para.6.2).The cushiongrip length shall be at least 60% of the handle length,and there shall be no detectable slippage between thehandle and the cushion grip under normal usage. Ahandlc with a cushion grip shall meet the dimcnsionalrequirements for the corresponding conventional typehandle for cach type and design (see Table 1).
5.6 WORKMANSHIP
The screwdriver shall be free from conditions whichmay impair its serviccability, durability or comfort.
6 TEST PROCEDURES
Many tests required herein are inherently hazardous,and adequate safeguards for personnel and propertyshall be cmployed in conducting such tests. The following tests are intended to ensure conformance with theperformance requirements of this Standard.
6.1 Visual Examination
Conformance with marking and other requirementsnot established by test shall be verified by visualexamination.
6.2 Hardness Test
Thc Rockwcll hardness tcst shall be conducted inaccordance with ASTM E 18. The Store duromctcrtest shall be conducted in accordance with ASTMD 2240.
6.3 Tip Torsional Test
The tip of each sample under test shall be locatedin a test block of applicable dimensions shown in theperformance section of Table 2 and Figs. 5A and 5B.When tested to the minimum tip torquc value specifiedin Table 2 neither the shank nor the tip shail showvisible permanent deformation.The torque shall be
ASME B107.15:2002 pdf free download
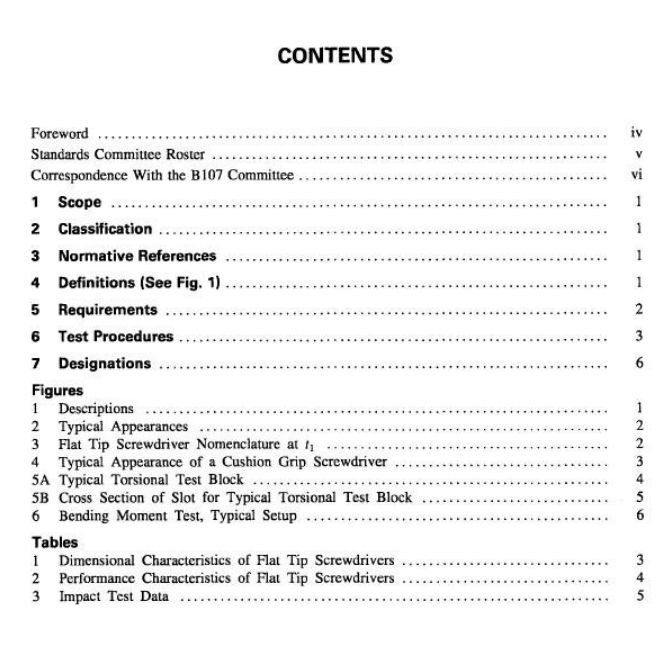