ASME A112.4.14:2004 pdf free download Manually Operated, Quarter-Turn Shutoff Valves for Use in Plumbing Systems
2GENERAL CONSTRUCTION AND ASSEMBLY2.1 General
Samples for testing to this Standard shall be randomlyselected from a lot of production representative samples.2.2 End Connections
2.2.1 Taper Pipe Threads. Metallic taper pipe threadsshall be in accordance with ASME B1.20.1. Plastic taperpipe threads shall be in accordance with ASTM F1498.2.2.2 Solder Connections. Solder-cup ends for coppertube connection shall be in accordance with ANSI Bi6.18or ASME B16.22.
2.2.3 Solvent Cement Connections.Socket ends forsolvent-cement connection to PvCor CPvC pipe or tubeshall be in accordance with ASTM D2466 (PvC andCPvC),ASTM D2467 (PVC),ASTM D2846 and ASTMF439(cPvc).
2.2.4 PEX Barbs Connection. Metallic barb-ends forconnection to PEX tubing shall be in accordance withASTM F1807. Plastic barb-ends for connection to PEXtubing shall be in accordance with ASTM F2159 or ASTMF1960.
2.2.5 Flared Connection.Flared connections to coppertube shall be in accordance with ASME B16.26.
2.2.6 Grooved End. Grooved end connections shall bein accordance with AWWA C606.
2.2.7 Other Connections. Connection methods notspecified herein shall be in accordance with a nationallyor internationally recognized standard.
2.3 Operation
The valve shall require 1!/4 turn from the fully closedposition to the fully opened position, or from the fullyopened position to the fully closed position.The valveshall be constructed so that the operator can visuallydetermine that the valve is in the opened or closed posi-tion. When the valve is in the closed position, theoperating lever or flow indicator shall be perpendicularto the longitudinal axis of the valve.The stem flats orindicator on the top of the stem shall indicate that thevalve is in the opened or closed position when theoperating device has been removed.
3MATERIALS
The following requirements pertain to materials usedin valve body, bonnet, end pieces, pressure-containingparts, and wetted operating parts.
3.1 Copper Alloys
Copper alloys shall be minimum 58% copper and meetone of the following specifications:
ASTM B62 (C83600)
ASTM B584 (C84400)
ASTM B124 (C37000)
ASTM B16 (C36000)
ASTM B371 (C69430)
UNS C89831
UNS C89833
UNS C89837
UNS C89510
UNS C89520
ISO Cu Zn40 Pb2 CW617N
ISO Cu Zn36 Pb2 As CW602N
ISO Cu Zn39 Pb3 CW614N
3.2 Ferrous Alloys
Ferrous alloys shall be a 300 series stainless steel.
3.3 Polymeric Materials
(a) PEX cross-linked polyethylene shall conform to ASTM F876 or ASTM F877.
(b)Chlorinated polyvinyl chloride (CPvC) materialused for pressure containing parts shall conform toASTM D1784,Classification 23447.
3.4 Alternate Materials
Alternate equivalent materials used shall conform tonational or international standards for which mechani-cal and chemical data are available. Metallic alloys withan excess of 8% lead shall not be used in contact withpotable water.
3.5 Flux and Solders
Flux and solders containing more than 0.2% lead shallnot be used in contact with potable water.
4DESIGN REQUIREMENTS
4.1 Stem Design
The valve shall be designed so that the stem-seal alonedoes not retain the stem to prevent the removal of thestem while the valve is under pressure.
4.2 Temperature,Pressure Rating
Metallic valves shall have a minimum pressure ratingof 125 psi (862 kPa) and the minimum temperature rat-ing shall be 140°F (60°C) for continuous use and 180°F(82°C) for intermittent use.
4.3 Temperature and Pressure Rating
Polymeric valves shall have a minimum pressure rat-ing of 125 psi (862 kPa) and the minimum temperaturerating shall be 140°F(60°C) for continuous use and100 psi (689 kPa) at 180°F (82-C) for intermittent use.
5 QUALIFICATION TESTING
5.1 Hydrostatic Test
(a)Metallic Valves. The test valve shall be given ahydrostatic test at a pressure of two times its markedpressure rating. The test fluid shall be water. The testfluid temperafure shall be 140°F(60°C).The durationof the test shall be 1 min.
The ball or disc shall be in such a position during theshell test as to ensure full pressurization of the valve.(b) Polymeric Valves.Polymeric valves shall be hydro-statically tested to ASTM F1970, para.8.2.
5.1.1 Performance Criteria.The valve exterior shallshow no visible leakage. Leakage through the stem pack-ing shall not be cause for rejection as long as a packinggland adjustment stops the leakage.
5.2 Seat Test
5.2.1 Procedure. Following the shell test,the testvalve shall be given a seat test. The test shall be a hydro-static test at not less than 125 psi at 140°F (60°C) or themaximum rated pressure and temperature of the valve.The test pressure shall be applied successively on eachside of the closed valve for duration of not less than1 min.
Valves marked as one-way valves require a seat testonly in the direction of the flow.
5.2.2 Performance Criteria There shall be no visibleevidence of leakage through the disc or ball nor leakagepast the seat.
5.3 Cycle Test
5.3.1 Procedure. A production sample valve shallwithstand 1,000 cycles of operation from the fullyopened to the fully closed position at its continuousrated temperature not less than 140°F (60°C). The test isto be conducted with a hydrostatic pressure-differentialapplied across the closed disc / ball equal to the ratedworking pressure.Restrictan opening downstream of thevalve to a flow of approximately 2.5 gpm (9.5 L/min)during the open portion of the test.
ASME A112.4.14:2004 pdf free download
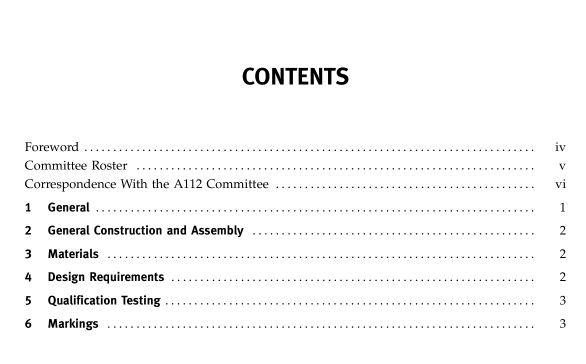