ASME B5.50:2015 pdf free download 7/24 Taper Tool to Spindle Connection for Automatic Tool Change
1GENERAL1.1 Scope
This Standard pertains to the standardization of basictoolholder shank, retention knob, and socket assembliesfor numerically controlled machining centers with auto-matic tool changers. The requirements contained hereinare intended to provide toolholder interchangeabilitybetween machining centers with automatic tool chang-ers of various types. This Standard is the inch solutionfor basic toolholder shank, retention knob, and socketassemblies. This design specifies an interchangeableretention knob with a 45-deg clamping surface.
Section 2 of this Standard specifies the dimensionsand tolerances of toolholder shanks having 7/24 tapersintended for automatic tool change. These are intendedfor use with the corresponding basic retention knob andspindle sockets specified in sections 3 and 4 (see Table 1).Section 3 contains information for standardization ofretention knobs for use with the 7 / 24 connection systemdescribed herein (see Table 2).
Section 4 specifies the dimensions and tolerances ofspindle sockets, drive keys, and key seats for machinetool spindles having 7/24 tapers intended for automatictool change (see Table 3 and Fig.1).These are intendedfor use with the corresponding basic toolholder shankand retention knob specified in sections 2 and 3.
1.2 Noninterchangeability
Tool shanks conforming to ASME B5.18-1972 (R2009)and ASME B5.40-1977 (R2013) are not interchangeablewith tool shanks established in this Standard.Toolshanks conforming to ISo 7388-1:1983 and retentionknobs per ISO 7388-2:1984, types A and B are not inter-changeable with this Standard.This also applies to addi-tional shank and knob designs that are in the draft stageswithin the ISO standards development system. Accord-ingly,the reader should note the warning statementincluded with the retention knob specifications shownin Table 2.
Some incompatibility with existing automatic toolchange arms may arise from dimension M (Table 1).1.3 Classification
This Standard covers a basic toolholder shank withan inch threaded retention knob with 45-deg clampingsurface that is applicable to general-purpose machining centers where loading and exchange of toolholders are
accomplished by automatic means. The term generalpurpose is intended to differentiate between machine
designs for unusually high accuracy requirements anddesigns intended to function with exceptionally highspindle rotational speeds coupled with higher axis feedrates, such as is normally found in high-speed machin-ing.Tool shanks made to this Standard may be usedwith a variety of proprietary retention and/or flangelocking systems.
1.4Definitions
autonatic tool changer(ATC): mechanism for the transferof the toolholder between a storage feature and the spin-dle or nonrotating socket.
balance: when the mass centerline and rotational center-line of a rotor are coincident.
basic cone: geometrically ideal conical surface that isgiven by its geometrical dimensions.These are a basiccone diameter, the basic cone length, and the basic rateof taper, or the basic cone angle.
basic foolholder shank: unit that fits directly into the spin-dle or nonrotating socket of the machine and has provi-sion for automatic tool change.
coolant hole: passage through the center of the retentionknob that allows through-the-spindle coolant to pass.This hole also permits access to a tool set height adjust-ment screw if so equipped.
drive key: device intended to assist in delivery of thedriving torque from the spindle nose to the tool.
effective case: depth within a metal part, measured fromthe part’s surface, where the minimum required hard-ness is present.
retention knob: member of the toolholder retention sys-tem that provides a coupling point between the tool-holder taper and the spindle drawbar.
spindle: component assembly of the machine tool, thefunction of which is to accept the basic toolholder shank.spindle nose: the part of a spindle into which the toolshank is accepted.
fool angular orientation: mechanical feature to positionand retain the basic toolholder shank in a specific angu-lar relationship to the spindle or nonrotating socket.fool shank: the part of a tool that mates with the taper
ASME B5.50:2015 pdf free download
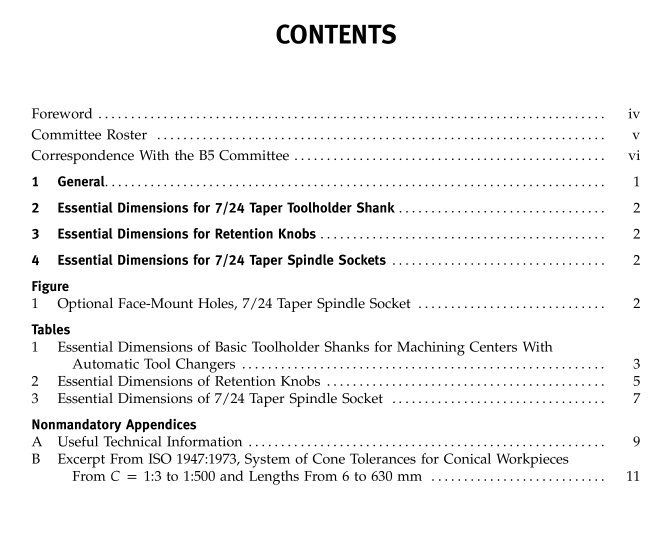