ASME B31G:2012 pdf free download Manual for Determining the Remaining Strength of Corroded Pipelines Supplement to ASME B31 Code for Pressure Piping
This document recommends a minimum safety factor equal to the ratio of the minimum hydrostatic test pres- sure required for the given type of pipeline construction to the MAOP or MOP, but usually not less than 1.25. Larger factors of safety may be appropriate in some cases, e.g., in locations of greater risk to the public or the environment.
Lesser factors ofsafety may be justified in some circumstances, e.g., for limited periods of time, or where additional procedures are in place to limit modes of operation, or in a remote location having reduced consequences of failure. In establishing the safety factor for a given pipeline segment, the pipeline operator shall give consideration to the accuracy of cor- rosion depth and length measurements, rates of corrosiongrowth, the characteristics ofthe pipe, the reliability of surge control or excess pressure limiting methods, and the presence of external factors that affect risk. When evaluating anomalies identified by inline inspection, use of larger factors of safety will result in smaller flaws being left in service following field investigation and pipeline repairs.
This can increase the reas- sessment interval to the next inline inspection.
1.10 Software The use of commercial or proprietary computer software packages, as well as purpose-written programs or spreadsheets, can greatly facilitate Level 1 evaluations, and is practically a necessity for conducting thorough Level 2 and Level 3 evaluations.
It is the user’s responsi- bility to verify the accuracy and reliability ofall software and spreadsheets, and to train personnel in their correct usage. Validation of software should include documented evidence that correct results are obtained over the full range of parameters that could reasonably be expected to occur when making evaluations.
The following document summarizes the results of burst tests and service failures of line pipe affected by corrosion or artificial metal loss, and which have previously been used for the purpose of validating the evaluation methods presented herein: Kiefner, J. F., Vieth, P. H., and Roytman, I., “Continued Validation of RSTRENG,” PRCI Catalog No. L51749, Contract PR 218-9304, Dec. 20, 1996.
Validation may be demonstrated by comparison of calculated results againstpublished benchmarktestdata such as that found in the above reference, or against results produced by another recognized evaluation method that have been calculated in accordance with this Standard. Validation ofthird-party software should also demonstrate that adequate checks or warnings are produced when parameters fall outside ranges that will ensure correct results.
1.11 Accuracy Consideration should be given to the accuracy of recorded flaw sizes, particularly where indirect methods are used to locate and size the flaws. Methods accounting for uncertainty in indirectly sized flaws include increasing the flaw dimension in order to account for detection tool error, or statistical analysis ofthe probable flaw sizes or risk of failure. Metal-loss corrosion anomalies indicated by inline inspection may be evaluated by a Level 1 or Level 2 evaluation method. The user is cautioned against over- stating the precision of evaluations applied with flaw dimensions indicated by inline inspection without adequate calibration or verification of actual flaw sizes by investigations carried out in the field.
1.12 Flaw Interaction The methods described hereinare suitable for evaluat- ing isolated areas of metal loss. Corrosion may occur such that multiple areas of metal loss are closely spaced longitudinally or transversely. If spaced sufficiently closely, the metal loss areas may interact so as to result in failure at a lower pressure than would be expected based on ananalysis ofthe separate flaws. The following guideline is suggested with reference to Fig. 1.12-1, based on limited testing and analysis:
ASME B31G:2012 pdf free download
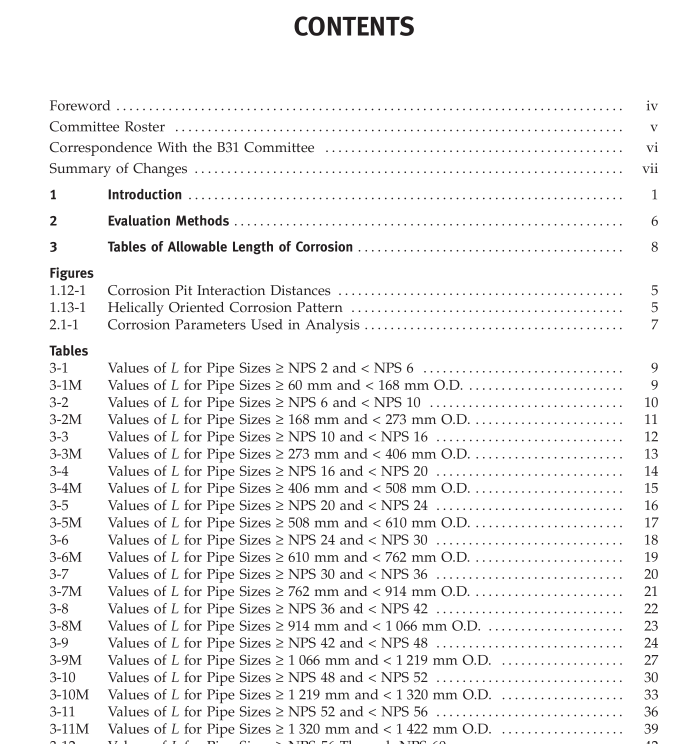